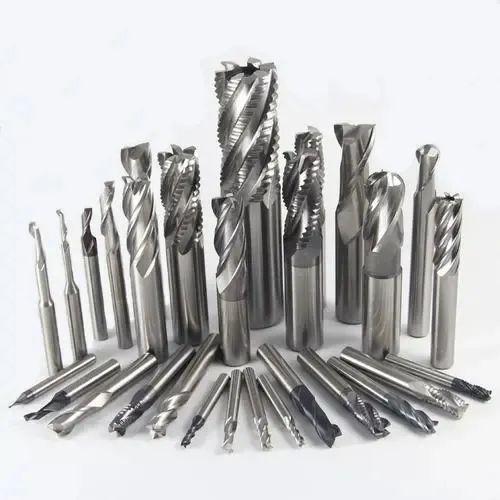
Moderné materiály na rezné nástroje majú za sebou viac ako 100 rokov vývoja od uhlíkovej nástrojovej ocele až po rýchloreznú nástrojovú oceľ,spekaný karbid, keramický nástrojasupertvrdé nástrojové materiályV druhej polovici 18. storočia bol pôvodným nástrojovým materiálom prevažne uhlíková nástrojová oceľ. V tom čase sa totiž používala ako najtvrdší materiál, ktorý sa dal obrábať na rezné nástroje. Avšak kvôli svojej veľmi nízkej teplote tepelnej odolnosti (pod 200 °C) majú uhlíkové nástrojové ocele nevýhodu v tom, že sa pri rezaní vysokými rýchlosťami okamžite a úplne otupujú v dôsledku rezného tepla a rozsah rezania je obmedzený. Preto sa tešíme na nástrojové materiály, ktoré sa dajú rezať vysokými rýchlosťami. Materiálom, ktorý odráža toto očakávanie, je rýchlorezná oceľ.
Vysokorýchlostná oceľ, známa aj ako predná oceľ, bola vyvinutá americkými vedcami v roku 1898. Nie je to ani tak o tom, že obsahuje menej uhlíka ako uhlíková nástrojová oceľ, ale o tom, že je do nej pridaný volfrám. Vďaka tvrdému karbidu volfrámu sa jej tvrdosť pri vysokých teplotách neznižuje a pretože sa dá rezať rýchlosťou oveľa vyššou ako je rýchlosť rezania uhlíkovej nástrojovej ocele, nazýva sa rýchlorezná oceľ. V rokoch 1900 až 1920 sa objavila rýchlorezná oceľ s vanádom a kobaltom, ktorej tepelná odolnosť sa zvýšila na 500 až 600 °C. Rýchlosť rezania ocele dosahuje 30 až 40 m/min, čo sa zvýšilo takmer 6-krát. Odvtedy sa so serializáciou jej základných prvkov vytvorili rýchlorezné ocele s volfrámom a molybdénom. Dodnes sa hojne používajú. Vznik rýchloreznej ocele spôsobil...
revolúcia v obrábaní reznými prvkami, výrazne zlepšila produktivitu obrábania kovov a vyžadovala si úplnú zmenu konštrukcie obrábacieho stroja, aby sa prispôsobil požiadavkám na rezný výkon tohto nového nástrojového materiálu. Vznik a ďalší vývoj nových obrábacích strojov následne viedol k vývoju lepších nástrojových materiálov a nástroje boli stimulované a rozvíjané. V podmienkach novej výrobnej technológie majú nástroje z rýchloreznej ocele tiež problém s obmedzenou životnosťou nástroja v dôsledku rezného tepla pri rezaní vysokou rýchlosťou. Keď rýchlosť rezania dosiahne 700 °C, rýchlorezná oceľ
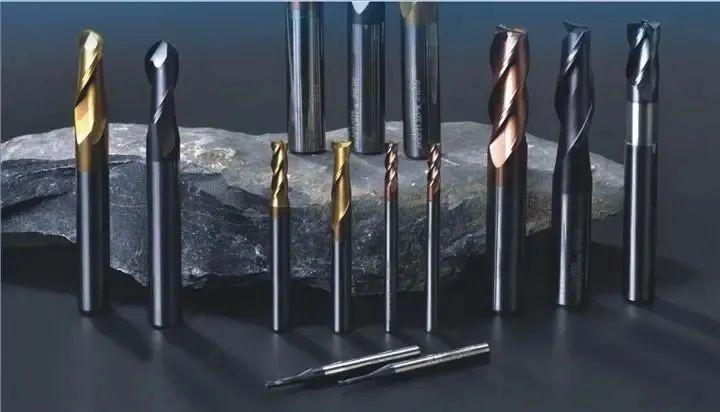
Hrot je úplne tupý a pri reznej rýchlosti nad touto hodnotou je úplne nemožné rezať. V dôsledku toho sa objavili karbidové nástrojové materiály, ktoré si zachovávajú dostatočnú tvrdosť aj pri vyšších teplotách rezania, ako sú uvedené vyššie, a je možné ich rezať pri vyšších teplotách rezania.
Mäkké materiály sa dajú rezať tvrdými materiálmi a na rezanie tvrdých materiálov je potrebné použiť materiály, ktoré sú tvrdšie ako diamant. Najtvrdšou látkou na Zemi je v súčasnosti diamant. Hoci prírodné diamanty boli v prírode objavené už dlho a majú dlhú históriu ich používania ako rezných nástrojov, syntetické diamanty boli úspešne syntetizované už začiatkom 50. rokov 20. storočia, ale skutočné využitie diamantov na širokú výrobu...materiály pre priemyselné rezné nástrojeje stále záležitosťou posledných desaťročí.
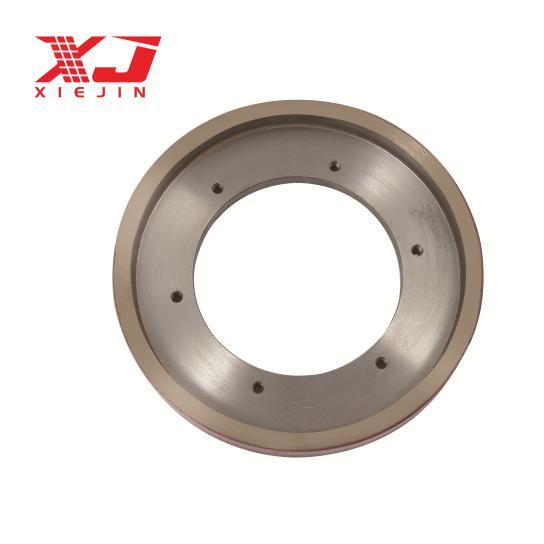
Na jednej strane, s rozvojom modernej vesmírnej technológie a leteckého priemyslu sa používanie moderných technických materiálov stáva čoraz hojnejším, hoci vylepšená rýchlorezná oceľ, spekaný karbid anové keramické nástrojové materiályPri rezaní tradičných obrobkov sa rýchlosť rezania a produktivita rezania zdvojnásobili alebo dokonca desiatkykrát zvýšili, ale pri ich použití na spracovanie vyššie uvedených materiálov je trvanlivosť nástroja a účinnosť rezania stále veľmi nízka a kvalita rezania je ťažko zaručiteľná, niekedy dokonca neschopná spracovať, čo vedie k potrebe použitia ostrejších a odolnejších nástrojových materiálov voči opotrebovaniu.
Na druhej strane, s rýchlym rozvojom modernejvýroba strojova spracovateľský priemysel, široké využitie automatických obrábacích strojov, obrábacích centier s počítačovým numerickým riadením (CNC) a bezobslužných obrábacích dielní, s cieľom ďalej zlepšiť presnosť spracovania, skrátiť čas výmeny nástrojov a zlepšiť efektivitu spracovania, sa kladú čoraz naliehavejšie požiadavky na odolnejšie a stabilnejšie materiály nástrojov. V tomto prípade sa diamantové nástroje rýchlo rozvíjajú a zároveň sa vyvíja aj vývoj...materiály diamantových nástrojovbol tiež výrazne propagovaný.
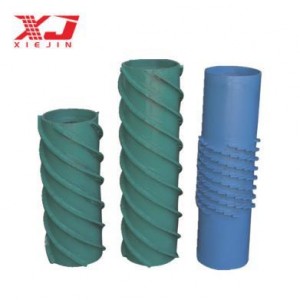
Materiály diamantových nástrojovmajú rad vynikajúcich vlastností s vysokou presnosťou spracovania, rýchlou rýchlosťou rezania a dlhou životnosťou. Napríklad použitie nástrojov Compax (polykryštalický diamantový kompozitný plech) dokáže zabezpečiť spracovanie desiatok tisíc dielov piestnych krúžkov zo zliatiny kremíka a hliníka bez toho, aby sa hroty nástrojov v podstate nezmenili; obrábanie hliníkových nosníkov lietadiel pomocou fréz Compax s veľkým priemerom môže dosiahnuť rezné rýchlosti až 3660 m/min; sú neporovnateľné s karbidovými nástrojmi.
Nielen to, použitiemateriály diamantových nástrojovmôže tiež rozšíriť oblasť spracovania a zmeniť tradičnú technológiu spracovania. V minulosti sa na zrkadlové spracovanie používal iba proces brúsenia a leštenia, ale teraz sa nielen používajú nástroje z prírodných monokryštálov diamantu, ale v niektorých prípadoch sa môžu použiť aj nástroje z PDC supertvrdých kompozitov na super presné a jemné rezanie, čím sa dosiahne sústruženie namiesto brúsenia. S použitímsupertvrdé nástrojeV oblasti obrábania sa objavili niektoré nové koncepty, ako napríklad použitie nástrojov PDC, kde limitujúcou rýchlosťou sústruženia už nie je nástroj, ale obrábací stroj, a keď rýchlosť sústruženia prekročí určitú rýchlosť, obrobok ani nástroj sa nezahrievajú. Dôsledky týchto prelomových konceptov sú rozsiahle a ponúkajú neobmedzené perspektívy pre moderný obrábací priemysel.
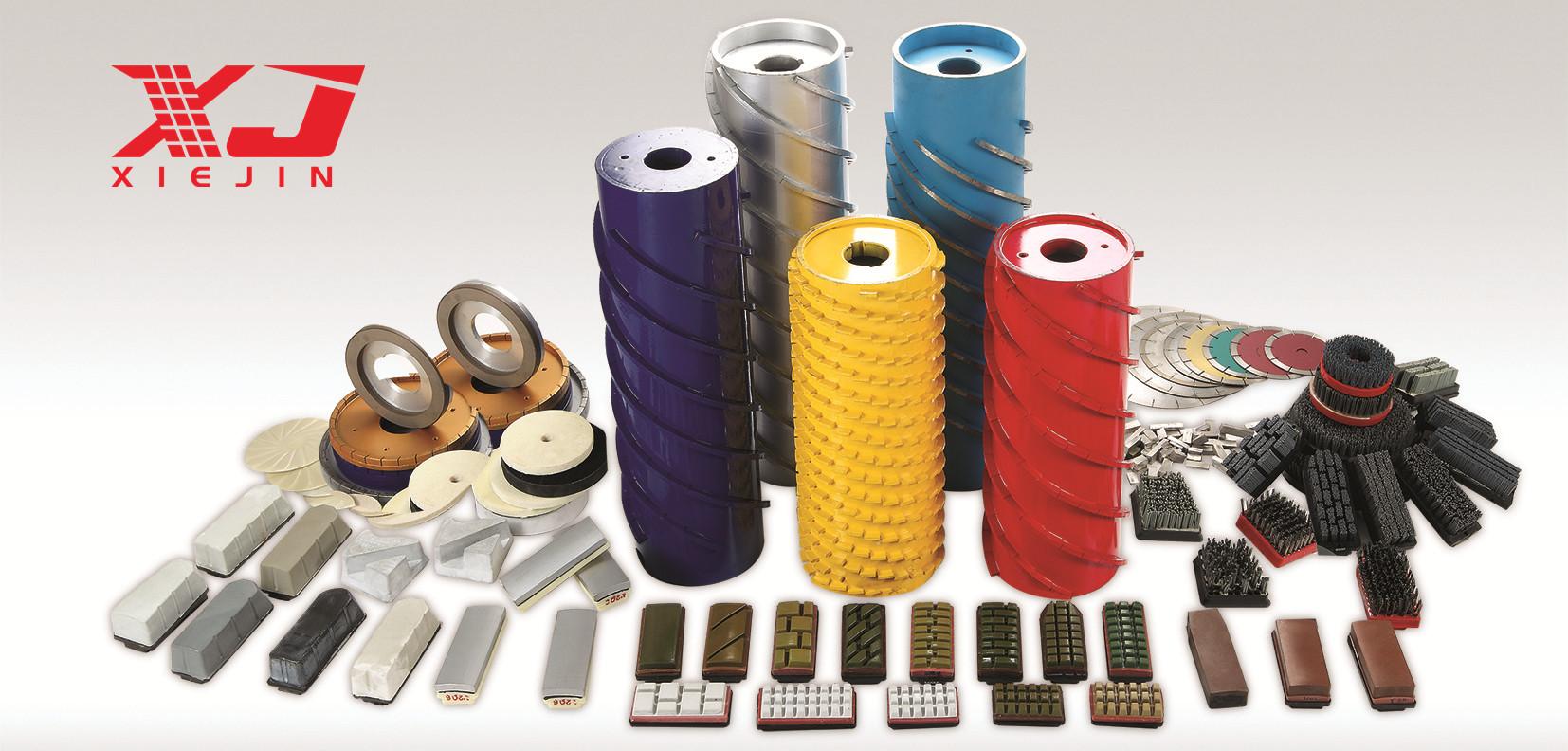
Čas uverejnenia: 2. novembra 2022